Chemical Reclassification: Triggers Every Safety Pro Should Know (2025 Update)
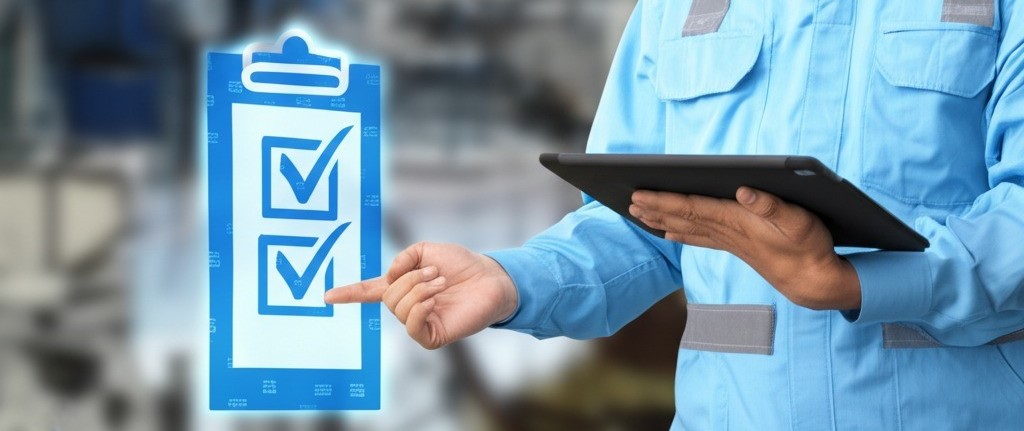
If you're like me, you've probably spent countless hours wrestling with SDSs, trying to figure out if a classification is still valid. Chemical reclassification isn't a "one-and-done" deal. It's an ongoing process, and assuming a classification remains valid forever is a dangerous – and potentially costly – mistake.
Just last month, I was working with a client who had a near-miss incident because a raw material's classification had changed, and they hadn't updated their SDS. Luckily, no one was hurt, but it was a wake-up call. Many companies are now using professional SDS creation platforms to help them stay current with classifications and avoid similar situations.
In this updated guide for 2025, I'll walk you through the critical triggers that must prompt a reclassification review. I'll share real-world examples from my experience and give you practical strategies to stay compliant and, most importantly, keep your workplace safe.
Why Reclassification Matters More Than Ever (Especially in 2025)
Let's be frank – keeping up with chemical regulations is getting harder, not easier. Here's what I'm seeing in the field that makes reclassification so crucial right now:
- Regulatory Updates are Accelerating: The UN's Globally Harmonized System (GHS) is constantly evolving (we're at Revision 10 now, published in 2023!). Plus, agencies like OSHA and ECHA are frequently updating their lists.
- Supply Chain Nightmares: Global supply chains are complex. A seemingly minor change in a raw material's source can have major classification implications, and you might not even get a clear notification.
- Enforcement is Getting Tougher: Regulators are cracking down on outdated SDSs. "Willful" violations (meaning you knew the SDS was outdated) carry hefty penalties. OSHA's updated Hazard Communication Standard (HCS), aligning with GHS Revision 7, has deadlines in 2026 and 2027 – are you ready?
- Evolving EU Standards: The EU is making big changes. The 2025 REACH revision brings in new ways to classify hazards.
I can't stress this enough: an outdated SDS isn't just a paperwork issue. It's a failure to communicate real hazards to your workers. Regulators see it that way, and so should you. This is why leading companies are now using AI-powered platforms to create and maintain their Safety Data Sheets in minutes, ensuring they always have the most current information.
Stay Ahead of Reclassification Requirements
Don't wait for a near-miss incident or regulatory inspection to update your hazard classifications. SDS Copilot's intelligent system monitors regulatory changes, tracks formulation adjustments, and automatically flags products that need reclassification. Create and update professional Safety Data Sheets in minutes with built-in compliance checks for GHS, OSHA HCS, and REACH requirements.
Try SDS Copilot FreeThe Seven Critical Reclassification Triggers (Updated for 2025)
1. Formulation Changes (Even "Tiny" Ones)
I've seen it happen too many times – a seemingly insignificant formulation tweak that completely changes a product's hazard profile. A tiny shift in concentration can push a product across a classification threshold.
- Concentration Shifts: Even a 1-2% change can make a difference.
- Raw Material Swaps: "Chemically similar" doesn't mean "hazard identical."
- Additives and Processing Aids: Don't underestimate their impact.
My Practical Tip: I always implement a "change checkpoint." Any formulation change, no matter how small, triggers an automatic reclassification review before it's implemented. No exceptions. Modern SDS creation platforms can automatically flag threshold crossings when you adjust formulations, making this process much more efficient.
2. Raw Material Supplier Changes
This is a classic trap. Switching suppliers is common, but different manufacturing processes can lead to different impurity profiles, even if the materials seem identical.
- Different Production Methods: These lead to different impurities.
- Specification Variations: Ranges can vary between suppliers.
- Hazard Equivalence (or Lack Thereof): Technical equivalence doesn't guarantee it.
Real-World Example: I've seen companies using multiple suppliers for the same chemical, but without harmonizing the classifications across all their downstream products. That's a recipe for disaster. SDS Copilot's ingredient tracking system can help identify these discrepancies automatically by maintaining a central database of your raw materials and their hazard profiles.
3. Regulatory Updates and Reclassifications
This is a never-ending battle. Regulatory bodies are constantly updating lists and classifications. Here's what you need to watch:
- GHS Updates: Stay on top of the latest GHS revision (currently Revision 10).
- OSHA HCS Updates: Know the transition periods for the updated HCS (deadlines in 2026 and 2027).
- EU CLP & REACH: Monitor changes, including new hazard classes (like Endocrine Disruptors) and the 2025 REACH revisions. The EU Commission added a number of chemicals to Annex I of the Prior Informed Consent (PIC) Regulation as of January 2025.
- Authoritative Lists: Check lists like ECHA's C&L Inventory at least quarterly – I make it a habit.
- Substances Under Review: Pay extra attention to these.
Actionable Tip: I assign specific team members to monitor updates for our key chemicals. It's a simple way to stay proactive. Some companies are now using AI-powered SDS creation tools that automatically incorporate regulatory updates as they occur, drastically reducing this monitoring burden.
4. New Hazard Data Emerges
Science marches on. New studies can reveal previously unknown hazards, and you need to be aware.
- Toxicological Studies: Set up alerts for new data on your key ingredients.
- Industry Chatter: Pay attention to what industry associations are saying.
- "Weight-of-Evidence" Shifts: These can affect classification even if there aren't big headlines.
Pro Tip: I have a clear definition of what constitutes "significant" new data that triggers a reclassification review. It prevents overreacting and underreacting. The latest generation of SDS platforms can help by automatically scanning scientific databases for new toxicological findings on your ingredients.
5. Process or Application Changes
How you use or process a material significantly affects its hazard profile. Don't overlook this.
- Particle Size Changes: This can dramatically alter explosion hazards (especially with powders – I've seen it firsthand).
- New Application Methods: These can change exposure routes.
- Temperature Changes: Higher temperatures can create decomposition hazards you didn't have before.
Crucial Advice: Get your safety team involved in any process change discussions from the very beginning. Proactive reclassification is the only way to go. Creating professional Safety Data Sheets in minutes with the right tools means you can quickly update your documentation when processes change.
6. Incident Findings and Near Misses
These are your real-world warning signs. Treat them as potential classification errors.
- Unexpected Reactions: These are red flags.
- Industry-Wide Incidents: Look for patterns that might point to broader problems.
- Root Causes: Dig deeper than the immediate cause.
Case Study: I've seen incident investigations reveal previously underestimated hazards, leading to a complete review of all related material classifications. It's a valuable learning opportunity. Using an SDS creation system that can quickly regenerate multiple documents based on new hazard information can make this process much more manageable.
7. The Three-Year Rule (and Why It Matters)
Even if nothing seems to have changed, you must do regular reviews. This is my non-negotiable rule.
- Science Evolves: Our understanding changes even without explicit regulatory updates.
- Testing Improves: New methods can reveal hazards we missed before.
- Supply Chain Creep: Gradual changes can happen without you realizing it.
- I recommend shorter intervals for high-hazard or high-volume materials.
My Approach: I set up a rotating review schedule, with high-risk materials checked more frequently. It's the only way to prevent "classification drift." Modern SDS management platforms can automatically flag documents approaching their review date and streamline the review process by creating professional Safety Data Sheets in minutes.
My Field-Tested Reclassification Process
A trigger is useless without a solid process. Here's what I've found works best in the real world:
- Automated Workflows: Triggers should automatically kick off a review. No more relying on memory.
- Designated Owner: Assign a "classification owner." Accountability is key.
- Documentation System: Write down why you made a classification decision. This is critical for future reviews and audits.
- Verification Step: A second set of eyes catches mistakes. It's a simple but effective safeguard.
- Communication Plan: Make sure everyone who needs to know about a change is informed.
- Digital Tools: I'm a big believer in using chemical management software to automate tracking, updates, and notifications. AI-powered SDS creation tools that can generate compliant documentation in minutes are revolutionizing this aspect of safety management.
This framework isn't just about compliance. It transforms reclassification from a reactive headache into a proactive safety tool.
"A systematic reclassification process doesn't just improve compliance—it transforms hazard communication from a reactive burden into a proactive safety tool."
The Reclassification Ripple Effect
Reclassifying one raw material can have a domino effect. You need to plan for these downstream consequences:
One reclassification can mean updating:
- Dozens (or hundreds!) of finished product SDSs
- Workplace labels (everywhere!)
- Storage arrangements (think incompatibilities)
- Employee training materials
- Transportation documents
Here's how to manage the chaos:
- Maintain a "Chemical Genealogy": Know exactly which raw materials go into which finished products.
- Automated Triggers: When a component changes, automatically flag all dependent products.
- Standardized Communication: Use a template for internal updates to keep everyone on the same page.
- Prioritization Framework: Tackle the most critical changes first.
- Streamlined Documentation: Use tools that can quickly generate professional Safety Data Sheets in minutes to handle bulk updates efficiently.
This turns a potential nightmare into a manageable process. Modern SDS Copilot systems can map these relationships automatically and regenerate all affected documents when an ingredient changes.
Manage Downstream Effects of Reclassification
When one ingredient changes, the ripple effect can impact dozens or hundreds of products. SDS Copilot's intelligent chemical relationship mapping automatically identifies all affected products when a raw material is reclassified. Generate updated Safety Data Sheets in minutes for your entire product line, ensuring consistent hazard communication and regulatory compliance across your organization.
Try SDS Copilot FreeThe Real Cost of Missing Reclassification Triggers
Let's talk about the costs of not reclassifying, because they're far greater than the investment in a good system:
- Regulatory Penalties are Skyrocketing: Fines can be huge, especially for systemic failures.
- Customer Trust is Fragile: Outdated classifications can cost you contracts and damage your reputation.
- Incident Costs are Astronomical: Misclassification increases the risk of incidents, and the costs can be devastating.
- Retrofitting is Always More Expensive: Reactive updates are a time-consuming and costly nightmare.
- Business Interruptions: Product launches can be delayed, orders can be held up – it's a mess.
A proactive, sustainable system is the only cost-effective approach. It's an investment in safety and your business's future. Modern AI-powered platforms that can create professional Safety Data Sheets in minutes typically pay for themselves within months through reduced administrative burden and compliance-related costs.
Final Thoughts: From Compliance Headache to Safety Advantage
The best companies I work with don't see reclassification as a burden. They see it as an opportunity to learn more about the materials they handle and improve their safety culture. This shift in mindset is transformative, especially when supported by tools that streamline your chemical safety documentation process.
This guide is a starting point. You need to continuously adapt your processes, stay informed about regulatory changes (they're not slowing down!), and prioritize proactive hazard communication. It's not just about ticking boxes; it's about protecting people and your business.
If you are overwhelmed by the complexity of maintaining compliant SDSs, there are modern solutions that can help you create professional Safety Data Sheets in minutes. Reach out to talk about your specific situation and how we might streamline your chemical safety documentation process.