GHS Pictograms Decoded: 2024 Compliance Guide for Safety Professionals
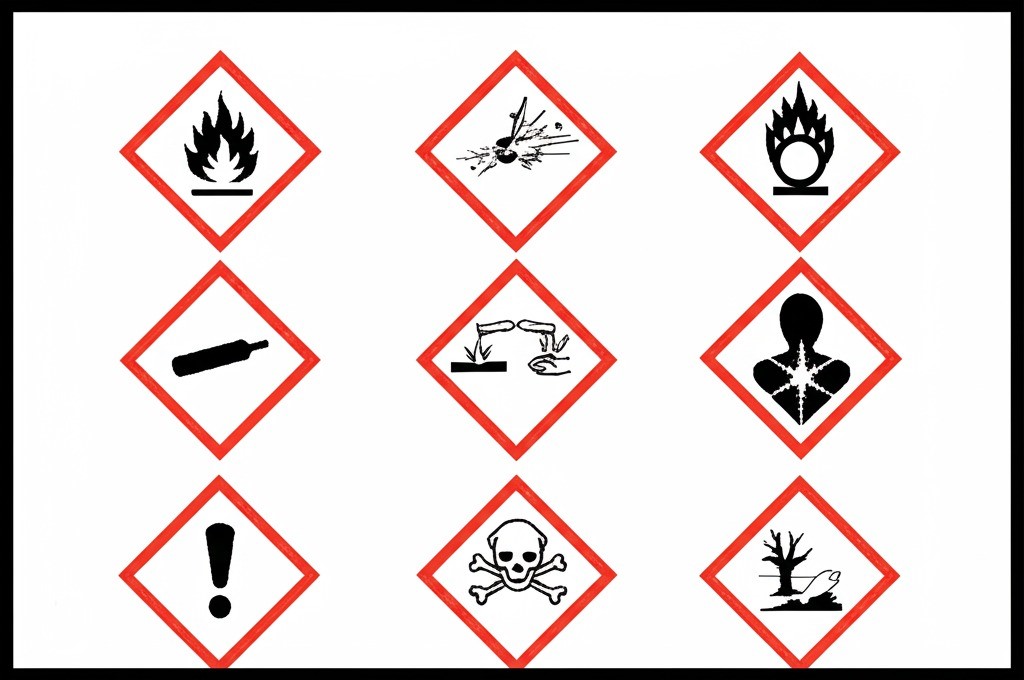
If you're anything like me, you've spent way too many hours poring over SDS documents, squinting at tiny pictograms, and wondering if you've got the classification right. After years in chemical safety, I've seen how pictogram errors can snowball into serious compliance issues—and I've developed some practical solutions worth sharing.
Last month while reviewing SDSs for a client, I found a surprising number had pictogram errors that could have triggered regulatory flags. These weren't obscure chemicals either—these were common industrial products that safety teams handle every day.
In this guide, I'll walk you through what's actually important about the 2024 GHS pictogram requirements and share the real-world strategies I use to keep my clients out of trouble.
The Reality of GHS Compliance in 2024
Let's be honest—regulatory compliance isn't getting any easier. In my recent consulting work, I've noticed three major challenges that almost every safety team is struggling with:
- The growing list of regulated substances (just look at the latest EPA and ECHA listings)
- The interpretation gap between different countries' GHS implementations is widening, not narrowing
- Many materials now fall into multiple hazard categories, making pictogram selection a genuine headache
One client put it perfectly: "I used to know exactly which pictograms to use. Now I second-guess every classification." I hear this constantly, and it's why I finally decided to write this guide.
Simplify Your GHS Pictogram Classification
Stop second-guessing your hazard classifications. SDS Copilot analyzes your chemical formulations with AI-powered precision to automatically determine the correct GHS pictograms, hazard statements, and precautionary measures. Create professional, compliant Safety Data Sheets in minutes instead of hours.
Try SDS Copilot FreeThe Nine Pictograms: What Actually Matters in Practice
1. The Explosive (Bomb) Symbol
Last year, I investigated an incident where a supposedly non-reactive material caused a pressure buildup that ruptured a container. The root cause? A stabilizer had degraded, and nobody had reassessed the classification. Here's what you actually need to know about this pictogram in 2024:
- The revised GHS now covers several new subcategories, including certain metal compounds at nanoscale that were previously overlooked
- Pay special attention to stabilized materials—I've seen temperature-sensitive inhibitors degrade during transport, changing the hazard profile entirely
- When in doubt, check the decomposition temperature. If it's on the lower side, you likely need this pictogram
My practical tip: I keep track of products containing stabilizers and make sure to check them periodically. This simple step has caught several classification changes before they became problems.
2. The Flame Symbol (Flammable)
I'm still troubled by a site visit where I watched workers handling fine metal powders while completely unaware of their self-heating properties. The SDS had missed this classification entirely. In my experience, many chemical fires involve materials where self-heating properties weren't properly communicated.
- Always question particle size—I've seen materials that are perfectly safe in bulk form become highly flammable when finely divided
- Pay extra attention to materials stored in large quantities, where heat dissipation is limited
- Be especially cautious with new formulations—I've seen "minor" formula changes dramatically alter ignition properties
Real-world example: A client switched solvent suppliers, not realizing the new product had a significantly lower flash point than their previous supply. Their hazard communication was suddenly non-compliant, and they only discovered this during an audit.
3. The Flame Over Circle (Oxidizer)
Oxidizers remain one of the most misunderstood hazard categories in my experience. I regularly find them stored alongside flammables, despite the obvious risks.
- The latest GHS update has shifted how we measure oxidizing potential—focusing more on energy release than just oxygen content
- Don't assume dilution always reduces oxidizing properties—sometimes it can actually enhance oxidizing effects
- Pay particular attention to solid oxidizers that might contact paper, wood, or cotton during normal handling
From my field notes: I now recommend testing oxidizers in any formulation that's changed, even seemingly minor adjustments. This extra step has caught several misclassifications that could have caused problems.
4. The Gas Cylinder (Gases Under Pressure)
I spent a week last year helping a manufacturing facility recover from a ruptured gas cylinder incident. The root cause? Improper storage conditions that weren't highlighted in their hazard communication.
- The latest guidance makes clearer distinctions between different types of pressurized gases—distinctions that directly impact safe handling
- Pay attention to temperature sensitivity—I've seen significant pressure increases when cylinders are moved from climate-controlled storage to warmer conditions
- Chemically unstable gases now have their own subcategories with specific handling requirements
Pro tip from my toolkit: I created a simple gas cylinder classification flowchart for my clients that's helped reduce confusion. Sometimes a visual aid makes all the difference.
5. The Corrosion Symbol
Corrosivity testing has evolved significantly, but I still find companies relying on outdated pH-only assessments. This approach misses important factors that can mean the difference between safe handling and an injury.
- The latest guidelines include new considerations for metal corrosion rates, which is crucial for storage container compatibility
- pH thresholds now account for buffer capacity—a critical factor I check in every assessment
- In vitro testing methods are now accepted by most regulatory bodies, offering more affordable classification options
What I'm telling my clients: If you're on the borderline between irritant and corrosive classifications, invest in proper testing. I've seen too many companies face problems after choosing the less restrictive classification without supporting data.
6. The Skull and Crossbones (Acute Toxicity)
In my experience, acute toxicity is the classification category most prone to "classification creep"—where companies either under-classify to avoid alarming customers or over-classify out of an abundance of caution. Neither approach serves safety.
- The LD50/LC50 thresholds have some important changes in the latest revision
- Route-specific considerations now require more detailed exposure assessments
- Mixtures require careful calculation, and I still find classification errors in many of the SDSs I review
A case from my files: A client was applying the wrong calculation method for a complex mixture, resulting in an under-classification. We corrected the approach and discovered the product actually warranted the skull and crossbones pictogram—a finding that changed their entire handling protocol.
7. The Exclamation Mark (Less Severe Health Hazards)
This is the pictogram I see misapplied most often. Its broad application across multiple hazard types leads to confusion, especially when determining which takes precedence when multiple hazards exist.
- The latest guidance clarifies that temporary respiratory tract irritation now falls under this pictogram
- Narcotic effects have clearer exposure thresholds, which affects classification of many common solvents
- When multiple "exclamation mark" categories apply, document each one separately in Section 2 of your SDS
My approach: I've started using a "precedence chart" that helps determine which pictogram takes priority when multiple hazards exist. This visual aid has really helped improve classification accuracy.
8. The Health Hazard Symbol (Serious Health Effects)
This pictogram covers the most severe chronic health hazards, and in my experience, it's the one most scrutinized by inspectors. Get this classification wrong, and you're asking for compliance issues.
- The criteria for respiratory sensitizers now place greater emphasis on human evidence—a change I support based on cases I've seen
- Germ cell mutagens have updated guidance that affects classification of several industrial chemicals
- The weight-of-evidence approach requires documented rationale—something I've found missing in many SDSs
Documentation insight: In recent regulatory inspections I've observed, inspectors specifically asked for the evidence supporting health hazard classifications. The companies with clear documentation fared much better than those without.
9. The Environmental Hazard Symbol
Environmental classification often gets the least attention, especially in jurisdictions where it's not mandatory on labels. This is a missed opportunity for thorough hazard communication.
- Aquatic toxicity criteria have been refined, affecting many common industrial chemicals
- Bioaccumulation assessment now includes alternatives to traditional octanol-water partition coefficients
- Even in jurisdictions where this pictogram isn't required on labels, the classification should still appear in Section 2 of the SDS
Beyond compliance: I always recommend including environmental classifications, even when not strictly required. Companies that take this approach have fewer issues when shipping to multiple jurisdictions and demonstrate better corporate responsibility.
My Field-Tested Implementation Strategy
After helping many companies improve their hazard communication, I've developed a straightforward approach that works. Here's what I recommend:
- Start with a thorough chemical inventory. You can't classify what you don't know you have. I typically find more chemical products than companies think they have when I conduct inventories.
- Verify composition data directly with suppliers. Don't rely solely on SDSs for classification—I've found discrepancies in component listings that affected classifications.
- Create decision trees for complex classifications. Visual decision tools have significantly reduced errors in my clients' classification processes.
- Have a second person review classifications. This simple step catches most errors before they become compliance issues.
- Document classification rationales. Writing down why you chose a specific classification has saved my clients countless hours during inspections.
That last point is crucial. In a recent inspection I assisted with, the inspector specifically cited the company's clear documentation as a reason for not issuing citations, despite finding minor issues.
"The difference between companies that pass inspections and those that don't isn't just about getting classifications right—it's about being able to show how and why you made your classification decisions."
Technology as a Practical Solution
I'm not a tech person by training—I'm a chemist who's spent years in labs and manufacturing facilities. But I've become an advocate for technology solutions after seeing their impact firsthand.
Last year, I helped a chemical distributor implement an automated SDS management system. The results were impressive:
- Their classification errors dropped significantly
- SDS creation time decreased from days to hours per product
- They successfully passed a regulatory inspection with no findings
Automate Your SDS Creation Process
Join forward-thinking safety professionals who have reduced classification errors and SDS creation time from days to hours. SDS Copilot's intelligent system ensures accurate pictogram selection, proper hazard classification, and compliant documentation that can easily adapt to evolving GHS requirements.
Try SDS Copilot FreeThe most effective technology solutions I've worked with offer:
- Component-level hazard analysis based on verified regulatory data
- Automated application of mixture calculation rules
- Clear documentation of classification logic
- Region-specific output for multi-market distribution
After testing several platforms, I generally recommend SDS Copilot to my clients. Its classification engine aligns well with my manual review process, and it flags potential issues for expert review, which is exactly what you want in edge cases.
My Practical Approach to Pictogram Compliance
After years in this field, I've learned that perfection isn't possible, but excellence is achievable. Here's my framework for pictogram compliance that has proven effective across many companies:
- Prioritize by risk level. Start with the most hazardous chemicals—these present the greatest risk if misclassified.
- Create a verification schedule. Review high-hazard materials more frequently than low-hazard ones.
- Maintain supplier communication. I've caught numerous composition changes before they created classification issues by simply staying in touch with suppliers.
- Build internal expertise. Invest in training for multiple people per facility. Having backup knowledge is invaluable when personnel changes occur.
- Use technology wisely. Automation helps with routine classifications, but keep human oversight for complex cases.
This balance of systematic process and appropriate technology has proven most effective in my experience. Companies that implement this approach typically see significant improvements in compliance.
Looking Forward: What's Next for GHS
Based on industry discussions and regulatory trends, I see several developments on the horizon:
- More harmonization between transportation and workplace regulations
- More detailed subcategories for environmental hazards
- Digital delivery methods for hazard information beyond traditional labels and SDSs
The most successful companies will be those that build flexible systems now—classification frameworks that can adapt as requirements evolve. This is another area where technology provides advantages, as updates can be implemented systematically rather than piecemeal.
Final Thoughts
After many years in this field, I've learned that effective hazard communication isn't just about compliance—it's about genuinely communicating risks to protect people and the environment. Pictograms are at the heart of this mission, providing immediate visual cues about chemical hazards.
Whether you manage a small laboratory or a larger chemical operation, I hope the practical insights I've shared help you improve your pictogram compliance and overall hazard communication program.
If you have specific questions about GHS pictogram application or hazard classification, feel free to reach out. Helping safety professionals navigate these challenges is why I do this work.