Common SDS Mistakes I Find in Every Audit
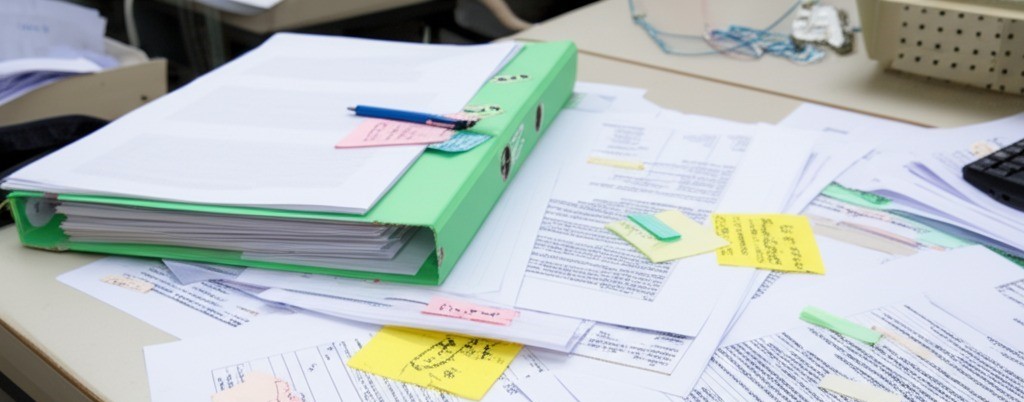
Having reviewed thousands of Safety Data Sheets throughout my career, I've developed a keen eye for compliance issues. It's not just that I find mistakes, but that I repeatedly encounter the same oversights, even within organizations that have well-established safety programs. This article reflects my findings as of March 2025.
Just last quarter, I performed a comprehensive SDS audit for a specialty chemical manufacturer confident in their "inspection-ready" documentation. Within hours, I'd identified over 40 critical compliance gaps that could have led to significant penalties. The safety manager was stunned—they'd been using the same SDS template for years, unaware of its fundamental flaws. Modern SDS creation tools like SDS Copilot could have prevented many of these issues through automated compliance checks.
In this article, I'll guide you through the most prevalent SDS mistakes I'm still seeing in 2025, explain why they are significant, and provide actionable steps to correct them before they escalate into major compliance problems.
The Evolving Landscape of SDS Compliance in 2025
Before we delve into specific mistakes, let's consider the current state of SDS management. The landscape has become increasingly complex due to:
- The accelerated pace of regulatory changes across global jurisdictions.
- The ever-increasing number of chemical substances that require thorough documentation.
- Heightened demands for transparency throughout the entire supply chain.
- Increased scrutiny from inspectors regarding the overall quality and accuracy of documentation.
One client recently confessed, "I used to be confident in our SDS library, but now I'm constantly worried we're just one inspection away from some serious findings." This is a common sentiment I hear from nearly every facility I visit, regardless of its size or industry. Many are now turning to AI-powered platforms that can create professional Safety Data Sheets in minutes to ensure compliance.
Save Time and Improve Accuracy
If you find yourself spending hours on manual SDS creation and management, our AI-powered SDS Copilot can automate this process with greater consistency and a clear audit trail explaining every decision point. Our system handles complex mixture calculations and regulatory logic, saving valuable time while ensuring compliance.
Try SDS Copilot FreeSeven Critical SDS Mistakes Still Prevalent in 2025
1. Discrepancies Between Section 2 (Hazards Identification) and Section 9 (Physical and Chemical Properties)
This lack of alignment between hazard statements and physical/chemical properties remains one of the most common issues. I estimate it appears in at least 60% of the SDSs I review.
Common errors:
- Flash points in Section 9 indicating flammability without corresponding flammability hazards in Section 2.
- pH values in the corrosive range (≤2 or ≥11.5) lacking corrosivity hazard classifications.
- Vapor pressure values that necessitate inhalation precautions, yet respiratory protection guidance is absent.
A recent example:
During an audit earlier this year, I discovered a solvent-based product with a flash point of 25°C (clearly a flammable liquids Category 2) that had no flammability hazard listed in Section 2. The company explained they had updated the formulation but only revised the physical properties section, neglecting the hazard classification. This oversight could have had severe repercussions.
My tip:
Develop a correlation matrix linking Section 9 properties to expected Section 2 classifications. A simple checklist can catch the vast majority of these inconsistencies. Alternatively, SDS Copilot automatically cross-references physical properties with hazard classifications to prevent these common discrepancies.
2. Incomplete or Overly Generic First Aid Measures (Section 4)
Section 4 should provide precise, product-specific guidance. Instead, I frequently find generic, unhelpful first aid instructions that offer little practical assistance in an emergency.
What I often see:
- Copy-pasted first aid measures that don't address the specific hazards of the ingredients.
- Vague instructions like "seek medical attention if necessary" without specifying when such attention is needed.
- Missing route-specific instructions for products with multiple potential exposure routes (e.g., inhalation, skin contact, ingestion).
An illustrative case:
I recently reviewed an SDS for a product containing phenol – a hazardous chemical requiring specific first aid – that stated only "flush with water". Phenol requires immediate and specialized medical intervention. Such a generalized instruction could lead to improper treatment and adverse outcomes.
Best practice:
Have a medical professional familiar with chemical exposures review your first aid measures. The most effective SDSs include clear triggers for seeking medical help and specific treatments that first responders should know. Modern SDS creation platforms can generate substance-specific first aid measures based on your formulation.
3. Incorrect Hazard Classification Based on GHS Calculation Methods
The Globally Harmonized System (GHS) provides specific mathematical formulas for classifying mixtures. However, companies often guess at classifications or use outdated methods.
Common shortcomings:
- Using simple addition of component percentages instead of the required GHS calculation methods.
- Failing to consider synergistic effects between components in the mixture.
- Not applying the correct cut-off values and concentration limits as specified by GHS.
Example:
A client was consistently underclassifying their products for skin irritation. They were using a calculation that considered components above a certain percentage, missing lower threshold GHS requirements. This resulted in a need to reclassify nearly half their product line.
My strategy:
I employ a tool that precisely applies the GHS algorithms for mixture classification, minimizing guesswork and ensuring compliance. Document each calculation step to demonstrate your due diligence. AI-powered SDS platforms can perform these complex calculations automatically, ensuring accuracy every time.
4. Missing or Imprecise Exposure Controls (Section 8)
Section 8 must provide specific details on exposure limits and protective measures. Often, it's either too generic or completely neglected.
Common deficiencies:
- Listing only OSHA Permissible Exposure Limits (PELs) when other occupational exposure limits (e.g., ACGIH Threshold Limit Values [TLVs], NIOSH Recommended Exposure Limits [RELs]) are more current and protective.
- Recommending personal protective equipment (PPE) that does not adequately address the identified hazards.
- Omitting engineering control recommendations for highly hazardous materials.
Impact:
I recently observed workers handling a corrosive substance with inadequate face protection, despite the SDS only listing basic eye protection. The SDS had failed to include appropriate face shield recommendations. Updating the documentation and implementing better controls immediately improved worker safety.
My advice:
Maintain a database of current occupational exposure limits from various organizations and regulatory bodies. Cross-reference each component against this database to ensure Section 8 reflects the most current and protective measures. This is an area where using an intelligent SDS generation system that maintains up-to-date regulatory data can really make a difference.
5. Overly Vague Incompatibility Information (Section 10)
Section 10 (Stability and Reactivity) should pinpoint specific materials and conditions to avoid. It often contains generic language offering little practical guidance.
Typical issues:
- Broad statements such as "avoid strong acids and bases" without further specifics.
- Missing details about commonly encountered materials that could trigger hazardous reactions.
- A lack of information about conditions (e.g., temperature, pressure, humidity) that can impact stability.
A cautionary tale:
A client experienced a near-miss when a worker stored incompatible materials together – both materials had SDSs, but neither SDS clearly communicated the specific incompatibility. Thorough and specific Section 10 information could have prevented the incident.
Recommendation:
Invest in chemical compatibility testing for new formulations and use precise language in Section 10. Instead of "incompatible with acids," specify: "incompatible with hydrochloric acid and nitric acid; reaction may generate toxic fumes." SDS Copilot draws from an extensive chemical reactivity database to provide specific incompatibility information based on your product's composition.
6. Outdated Regulatory Information (Section 15)
Regulatory requirements are constantly evolving, yet SDSs often contain Section 15 information that hasn't been updated in years.
Common problems:
- References to regulations that have been repealed or amended.
- Failure to include newly regulated substances or reporting requirements.
- Inaccurate or outdated California Proposition 65 listings.
An observation:
A recent audit revealed that a significant percentage of a company's SDSs contained regulatory information that was over a year out of date. In several cases, components had been added to restricted substance lists after the SDS was created, rendering their documents non-compliant.
My suggestion:
Implement a regulatory monitoring system that triggers automatic SDS reviews when relevant regulations change. For smaller companies, conduct a regulatory review of your high-volume products at least twice a year. Alternatively, consider a cloud-based SDS creation platform that continuously updates regulatory information, ensuring your documents remain compliant with minimal effort.
7. Deficient Document Control and Revision Practices
Even the most accurate SDS is problematic if you cannot demonstrate proper document control – something inspectors are increasingly focused on.
Frequently observed errors:
- Missing revision dates or a lack of revision history.
- Absence of a system to ensure that the most current version is readily accessible and in use.
- Inability to demonstrate that updates were made in response to specific new information or regulatory changes.
Important:
During a recent inspection, a company received a citation not because their SDSs were incorrect, but because they could not demonstrate a systematic approach to maintaining their SDSs and keeping them current.
A working solution:
Implement a formal SDS review protocol that includes:
- Scheduled reviews based on the level of risk (higher hazard = more frequent review).
- Triggered reviews whenever formulations are altered, regulations change, or new hazard information becomes available.
- A documented approval process with clearly defined roles and responsibilities.
- A robust distribution system that ensures outdated documents are removed from circulation promptly.
This systematic approach enhances compliance and demonstrates due diligence. Many forward-thinking companies are now using AI-powered SDS management systems that automatically track revisions and maintain a complete audit trail.
My Field-Tested SDS Audit Approach
Through numerous SDS audits, I've developed a methodical approach to identify common issues:
- Verify hazard assessments first. Confirm the accuracy of the hazard classification in Section 2 based on composition and properties.
- Cross-check for internal consistency. Ensure alignment between sections—hazards and precautionary statements, physical properties and hazard classifications, etc.
- Verify against source documentation. Compare the SDS to raw material SDSs, test data, and regulatory lists.
- Review for practical usability. Evaluate if the information is useful in an emergency—are first aid measures specific?
- Assess compliance with all applicable regulations. Check against GHS and jurisdiction-specific regulations.
This structured approach works across industries, from small manufacturers to multinational companies. Interestingly, many of these verification steps are now automated in modern SDS creation platforms, which can generate compliant Safety Data Sheets in minutes rather than the hours or days required for manual creation.
"The key to an SDS that passes inspection lies in attention to detail and a systematic verification process. It's about having the right information in the right place."
Leveraging Technology for SDS Management
I believe in using technology strategically. The most effective SDS management systems offer:
- Automated cross-referencing to flag inconsistencies.
- Regulatory monitoring with alerts.
- Formulation tracking for change management.
- Audit trails for compliance.
However, technology is not a complete solution. Combine technology with proper training and expertise. The most advanced SDS Copilot systems available today can create professional Safety Data Sheets in minutes while ensuring compliance with global regulations, but they still benefit from expert oversight.
Save Time and Improve Accuracy
If you find yourself spending hours on manual classification, our AI-powered SDS Copilot can automate this process with greater consistency and a clear audit trail explaining every decision point. Our system handles complex mixture calculations and regulatory logic, saving valuable time while ensuring compliance.
Try SDS Copilot FreeImmediate Steps for SDS Improvement
Here are steps you can take now:
- Conduct a sample audit. Review a selection of SDSs for the outlined issues.
- Create a standardized review checklist. Tailor a checklist to address common mistakes and industry-specific concerns.
- Implement peer reviews. Have a second set of eyes review each SDS.
- Develop a trigger list for updates. List events that trigger an SDS review.
- Document your rationale. Keep records of classification decisions.
- Consider automation. Explore AI-powered platforms that can streamline your chemical safety documentation process and eliminate common mistakes.
Companies that implement these practices see a significant decrease in SDS compliance issues. Those that additionally leverage intelligent SDS creation tools often report up to 90% time savings in their documentation processes.
Future Trends in Safety Data Sheets
I foresee the following developments:
- A move toward digital formats with interactive elements.
- Greater emphasis on exposure scenarios and real-world applications.
- More stringent requirements for nanomaterials and emerging chemicals.
- Increased global harmonization with streamlined cross-border compliance.
- Wider adoption of AI-powered SDS creation systems that can generate compliant documentation in minutes rather than days.
The best-prepared companies will view SDSs as dynamic documents within a management system, leveraging technology to ensure ongoing compliance while reducing administrative burden.
Conclusion
I view SDSs as vital communication tools that protect workers and the environment. Proper SDSs are an effective hazard communication method, and creating them shouldn't consume excessive time and resources when modern solutions can generate professional Safety Data Sheets in minutes.
Whether you manage a few products or thousands, I hope these insights improve your SDS quality. The mistakes I've outlined are preventable, especially when you leverage the right tools and expertise.
Feel free to reach out with questions about SDS compliance or how to streamline your chemical safety documentation process. Helping safety professionals is a rewarding part of my job.