The SDS Audit Survival Guide: Common Mistakes, Best Practices, and How to Prepare
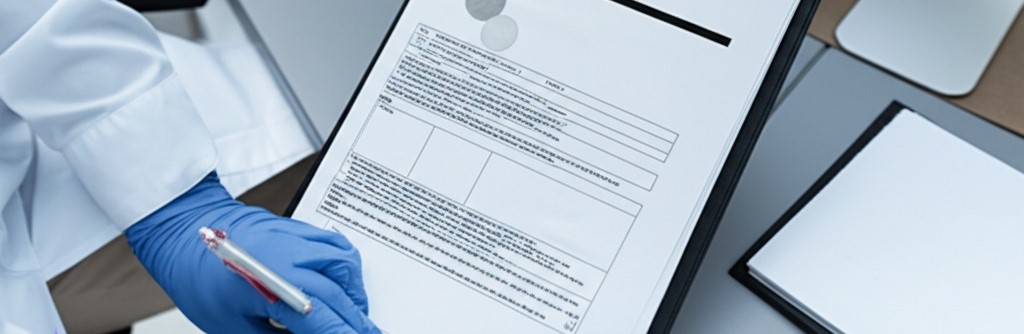
After conducting hundreds of SDS audits over my career, I've witnessed the same critical compliance gaps across organizations of all sizes. Despite best intentions, many safety professionals struggle to maintain comprehensive SDS documentation that satisfies regulatory scrutiny. This guide shares the most common audit findings I encounter and provides a systematic framework for transforming your SDS management from a reactive compliance burden into a proactive safety system.
The Audit Reality: Common SDS Failures That Trigger Citations
When regulatory inspectors examine your SDS documentation, they're looking beyond simple paper compliance to evaluate your overall chemical safety management system. Based on my experience, these are the most frequent compliance failures that result in citations:
Incomplete or Inconsistent Information
The most prevalent issue I identify during audits is incomplete or inconsistent information that undermines SDS effectiveness as safety communication tools. Many organizations maintain documents with missing sections, incomplete hazard information, or outdated regulatory references that fail to align with current standards.
During a recent audit at a manufacturing facility, I found that over 40% of their SDSs were missing critical information in Section 8 (Exposure Controls/Personal Protection). This created significant safety risks, as employees lacked comprehensive information needed to select appropriate PPE. The resulting citations required extensive corrective action that could have been avoided through proactive documentation review.
Chemical Misclassification and Labeling Discrepancies
Another critical error frequently highlighted during audits is the misclassification of chemicals, which leads to inappropriate labeling and inadequate risk management practices. When hazardous substances are incorrectly classified, organizations implement insufficient safety protocols that leave workers vulnerable to health risks.
I regularly find discrepancies between the classification information in Section 2 of the SDS and the actual warning labels applied to chemical containers. These inconsistencies not only trigger citations but also indicate deeper problems with hazard communication that could contribute to workplace incidents.
Accessibility and Employee Knowledge Gaps
One of the most overlooked aspects of SDS compliance is accessibility. Regulatory requirements mandate that Safety Data Sheets be "readily accessible" to employees during all work shifts when they may be exposed to hazardous chemicals.
During audits, I test this by asking random employees to demonstrate how they would access the SDS for chemicals in their work area. In approximately 60% of facilities, employees either cannot locate the documentation or require excessive time to retrieve it—a clear violation that attracts immediate regulatory attention.
Inventory Discrepancies
Perhaps the most fundamental audit finding involves gaps between the chemical inventory and available SDS documentation. Many organizations cannot produce Safety Data Sheets for all hazardous chemicals present in their facility, while simultaneously maintaining outdated SDSs for products no longer in use.
This inventory-documentation mismatch creates significant compliance vulnerabilities and suggests inadequate chemical management systems. Auditors typically identify these gaps by conducting spot checks of storage areas and comparing findings against the master SDS list—a practice I recommend organizations implement internally before external auditors arrive.
Are You Audit-Ready?
Don't wait for inspectors to find gaps in your documentation. SDS Copilot generates professional Safety Data Sheets in minutes with AI-powered hazard classification, GHS-compliant templates, and automated updates. Create compliant SDSs, track your inventory, and maintain a comprehensive audit trail to demonstrate regulatory due diligence.
Try SDS Copilot FreeBuilding Your Audit-Ready SDS Management System
Step 1: Establish a Comprehensive Chemical Inventory
The foundation of any audit-resistant SDS management system begins with creating a comprehensive baseline inventory of all hazardous chemicals present within your facility. This inventory serves as the cornerstone of compliance, allowing you to systematically track which substances require Safety Data Sheets and verify documentation completeness.
To establish an effective inventory:
- Conduct thorough facility walk-throughs examining storage areas, production floors, laboratories, and maintenance departments
- Document every chemical product including regularly used chemicals, occasionally used substances, samples, and chemicals in storage
- Record key information including product name, manufacturer, part/catalog number, location, quantity, and date received
- Identify responsible departments to enable targeted follow-up during reconciliation activities
This baseline inventory becomes your verification tool during audits, allowing you to demonstrate systematic chemical management rather than haphazard documentation practices.
Step 2: Implement a Structured SDS Receipt and Review Process
Once you've established your inventory, implementing a structured SDS receipt and review process becomes essential for maintaining compliance. This process should include:
- Verification of completeness: Confirm that each SDS contains all 16 required sections
- Language assessment: Verify that the document is in the appropriate language for your workforce
- Date validation: Check that the document includes accurate dating with revision information
- Matching verification: Ensure the SDS matches the exact product you've received (including formula version)
- Integration with inventory: Update your master chemical list when adding new SDS documents
Establish clear procedures for contacting suppliers when SDS information appears incomplete or inaccurate, documenting these communications as evidence of due diligence during audits. This systematic approach prevents non-compliant documentation from entering your system and creating downstream compliance vulnerabilities.
Step 3: Develop Robust Document Management Practices
Systematic document management constitutes another crucial element of audit preparation. Organizations must maintain records of both current and archived versions of Safety Data Sheets, establishing clear filing systems that facilitate quick retrieval during inspections.
Your documentation system should include:
- Version control: Maintain both current and archived versions with clear dating
- Organized storage: Structure your filing system (physical or electronic) logically by location, department, or hazard category
- Regular reviews: Establish schedules for verification that SDSs remain current (at least every five years)
- Update protocols: Define processes for implementing revision updates when manufacturers provide them
- Archiving procedures: Maintain historical documentation for discontinued products (30 years under OSHA)
During audits, this systematic approach demonstrates to inspectors that you've implemented thoughtful compliance systems rather than simply collecting documents without structure or purpose.
Step 4: Ensure Universal Accessibility
Accessibility represents a frequently overlooked aspect of SDS management that often triggers audit findings. Regulatory requirements typically mandate that Safety Data Sheets be "readily accessible" to employees during all work shifts when they may be exposed to hazardous chemicals.
To satisfy this requirement:
- Assess work environments: Consider factors like computer access, literacy levels, and multiple work locations
- Implement appropriate systems: Deploy paper-based, electronic, or hybrid solutions based on your assessment
- Provide multiple access points: Ensure documentation can be accessed from all relevant work areas
- Test accessibility: Regularly verify that employees can quickly locate SDSs for chemicals in their work area
- Document your approach: Maintain records explaining your accessibility decisions
By documenting your accessibility strategy, you demonstrate to auditors that you've thoughtfully addressed this requirement rather than simply assuming compliance.
Ensure SDS Accessibility Across Your Organization
Our AI-powered SDS Copilot provides universal access to your safety documentation from any device, ensuring employees can instantly retrieve critical chemical information wherever they work. Our system maintains a complete audit trail of SDS access, helping you demonstrate compliance with regulatory accessibility requirements while providing powerful search capabilities that make finding specific chemical information effortless.
Try SDS Copilot FreeCritical SDS Sections That Attract Auditor Scrutiny
During audits, regulatory inspectors typically focus particularly intensive scrutiny on several key sections of Safety Data Sheets that directly impact worker safety. Understanding these focus areas allows you to prioritize your compliance verification efforts.
Section 2: Hazard Identification
This section receives priority attention, as it contains critical information about chemical dangers that drives downstream safety decisions. Auditors evaluate whether:
- Hazards are correctly classified according to applicable standards
- Information aligns with the chemical's actual composition in Section 3
- Identified hazards correspond appropriately with precautionary measures
- Pictograms and signal words match the classification statements
To prepare for this scrutiny, conduct detailed reviews of Section 2 for each SDS, ensuring accuracy and consistency with both regulatory requirements and the actual properties of the substances you handle. Pay particular attention to alignment between this section and your workplace labeling systems.
Section 8: Exposure Controls/Personal Protection
This section represents another critical audit focus area, as it directly connects hazard information to practical protective measures. Regulatory inspectors examine whether:
- Recommended exposure controls reflect current best practices
- Personal protective equipment specifications provide adequate worker protection
- Occupational exposure limits are current and appropriate
- Engineering controls are adequately described
Auditors frequently cross-reference this information with your organization's actual practices, looking for discrepancies between documented recommendations and implemented controls. Systematically verify alignment between SDS recommendations in this section and your organization's chemical handling procedures, addressing any gaps before auditors identify them.
Sections 4-6: Emergency Response Information
These sections attract significant audit attention due to their implications for worker safety during incidents. Auditors evaluate whether:
- First-aid measures provide specific, actionable guidance
- Firefighting measures include appropriate extinguishing media and specific hazards
- Accidental release measures address containment and cleanup procedures
- Information aligns with your emergency response plans and training
To prepare for this scrutiny, ensure these sections contain specific, practical information rather than generic statements, and verify that your emergency response protocols correspond to the guidance provided in these SDS sections.
Section 3: Composition/Information on Ingredients
The composition information undergoes particularly rigorous examination during audits, especially for manufacturers and importers. Regulatory inspectors evaluate whether:
- All hazardous ingredients are appropriately disclosed according to relevant concentration thresholds
- Identified components align logically with the hazard classifications in Section 2
- CAS numbers and chemical identifiers are accurate and consistent
- Trade secret claims follow regulatory requirements for substantiation
While downstream users bear less responsibility for the technical accuracy of this section, you should nevertheless review it critically when receiving new chemicals, questioning suppliers about any apparent inconsistencies between composition information and observed product properties or effects.
Best Practices for Ongoing SDS Compliance
Regular Verification Processes
Implementing regular verification processes stands as a cornerstone of SDS compliance best practices. Safety professionals should:
- Conduct periodic spot checks of the chemical inventory against the master SDS list
- Perform random physical inspections of chemicals on the shop floor, comparing actual products with inventory records
- Implement tracking systems such as barcode or QR code systems for efficient verification
- Document all verification activities with dates, findings, and corrective actions
These verification processes demonstrate proactive compliance management to auditors while preventing the inventory-documentation gaps that frequently trigger citations.
Comprehensive Employee Training
While having accurate documentation is essential, ensuring that workers understand how to access and interpret this information proves equally important from a regulatory perspective. Comprehensive training programs should cover:
- The location and accessibility of SDSs throughout the facility
- The structure and content of these documents, with emphasis on safety-critical sections
- How to extract information relevant to specific job functions
- Procedures for requesting missing documentation or reporting concerns
Document this training thoroughly, including attendance records, content outlines, and competency assessments that demonstrate employees' practical understanding of SDS utilization for daily safety practices and emergency response.
Supplier Management Practices
Supplier management practices significantly impact SDS compliance, particularly regarding the handling of chemical samples, new products, and updated formulations. Best practices include:
- Establishing clear procedures prohibiting acceptance of any chemical materials without accompanying SDSs
- Implementing formal request processes for obtaining updated documentation from manufacturers
- Documenting all communication regarding SDS requests and follow-up
- Training receiving personnel on verification procedures for incoming chemicals
This systematic approach prevents undocumented chemicals from creating compliance gaps that auditors quickly identify during inspections.
Documentation of Compliance Efforts
Documentation of compliance efforts provides critical evidence during audits that your organization has exercised "reasonable diligence and made good faith efforts" to maintain SDS compliance. Maintain comprehensive records of:
- Inventory reconciliation efforts and findings
- Supplier communications regarding documentation requests
- Internal audits of SDS systems and results
- Corrective actions taken to address identified deficiencies
- Employee training on SDS access and utilization
These records demonstrate a proactive compliance approach rather than reactive crisis management, significantly influencing auditors' overall assessment of your safety culture and commitment to regulatory requirements.
Implementing an Effective SDS Management System
Defining Roles and Responsibilities
Establishing a robust SDS management process begins with defining clear roles and responsibilities throughout the organization. Successful implementation requires designating specific individuals accountable for various aspects of compliance, including:
- Inventory management: Maintaining the master chemical list
- Document receipt and review: Verifying SDS completeness and accuracy
- Accessibility maintenance: Ensuring documentation remains available to all workers
- Supplier communication: Obtaining updated documentation when needed
- Audit response: Coordinating information during regulatory inspections
These designations should extend beyond the safety department to include purchasing staff, receiving personnel, department managers, and executive leadership. Formal documentation of these responsibilities ensures systematic rather than haphazard SDS management.
Technology Solutions for Enhanced Compliance
Technology solutions can significantly enhance SDS management efficiency and compliance, though they require thoughtful implementation. Electronic SDS management systems offer advantages including:
- Centralized document storage with version control
- Automated update notifications from manufacturers
- Instant accessibility across multiple locations
- Simplified audit response through rapid search capabilities
- Integration with chemical inventory management
When implementing these systems, ensure they meet specific regulatory requirements regarding accessibility, backup provisions, and employee usability. Implementation should include thorough configuration to match your organization's chemical management workflows and comprehensive training for all system users.
Integration with Chemical Lifecycle Management
Integration of SDS management with broader chemical lifecycle processes represents a best practice that enhances both compliance and operational efficiency. Rather than treating Safety Data Sheets as standalone documentation requirements, incorporate them into comprehensive chemical management workflows that span:
- Purchasing approval processes that require SDS verification before ordering
- Receiving procedures that reject chemical deliveries without documentation
- Inventory tracking systems that link containers to specific SDS versions
- Hazard communication programs that leverage SDS information for training
- Disposal practices guided by SDS waste handling recommendations
This integration ensures that SDS compliance considerations influence decisions at each stage of chemical handling, preventing the compliance gaps that frequently occur when SDS management operates in isolation from operational chemical decisions.
Conclusion: From Compliance Burden to Strategic Advantage
Safety Data Sheet compliance represents far more than an administrative burden or regulatory checkbox—it constitutes a foundational element of comprehensive chemical safety management that protects workers, communities, and organizational sustainability. By addressing common audit findings before they occur, implementing robust verification processes, and integrating SDS information into operational decision-making, you can significantly reduce both compliance risks and actual chemical hazards within your facilities.
The investment required for establishing effective SDS management systems yields returns extending well beyond avoided regulatory penalties:
- Enhanced operational efficiency through reduced chemical management confusion
- Decreased incident rates resulting from improved hazard awareness
- Strengthened safety culture built on transparent information sharing
- Synergistic compliance benefits across multiple regulatory domains
As regulatory frameworks continue evolving globally, maintaining adaptable SDS management systems becomes increasingly important for forward-thinking organizations. By establishing fundamentally sound SDS processes built on the principles of comprehensive inventory management, systematic document control, universal accessibility, and continuous improvement, you position your organization to adapt efficiently to these evolving requirements while maintaining consistent protection for your workforce.