Mastering Mixture Classification: A Step-by-Step Guide to Accurate SDS Hazard Determination
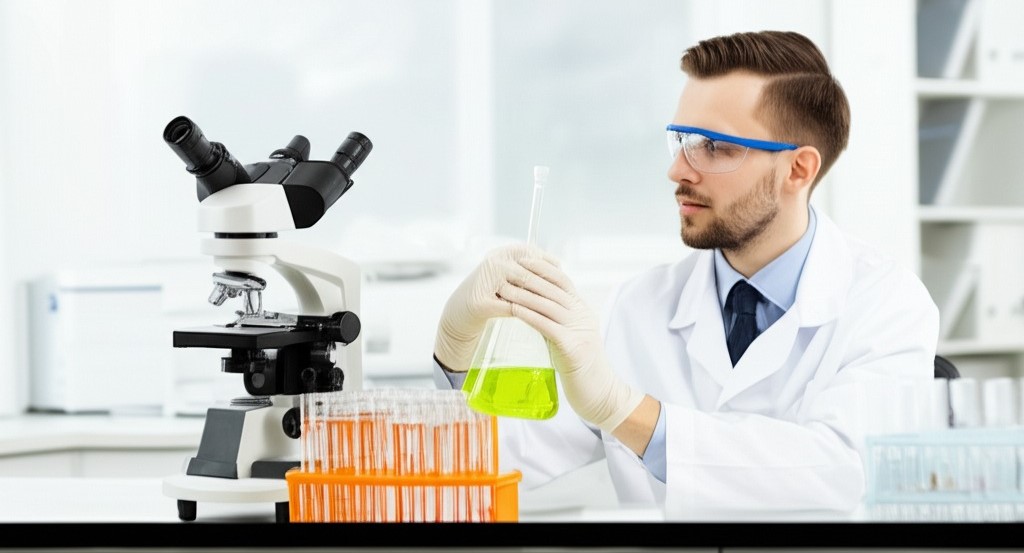
Chemical mixture classification represents one of the most challenging aspects of SDS development. In my twenty years as a chemical safety professional, I've witnessed countless organizations struggle with the complex calculations, decision trees, and judgment calls required to accurately classify mixtures under GHS. This guide distills my experience into practical approaches that will help you navigate the mixture classification maze while ensuring regulatory compliance and—most importantly—accurate hazard communication.
The Hierarchical Approach to Mixture Classification
GHS establishes a clear hierarchy for determining the hazard classification of mixtures, with three primary approaches in descending order of preference:
- Test data for the complete mixture – When reliable test data exists for the mixture as a whole, this takes precedence over all other methods
- Bridging principles – When test data exists for similar mixtures, bridging principles can be applied to classify untested mixtures
- Calculation methods – When neither complete mixture data nor bridging principles apply, ingredient-based calculations determine classification
In my auditing experience, I frequently encounter SDSs where this hierarchy is ignored or misapplied. Companies often default to the most accessible method rather than following the prescribed sequence. For example, many safety professionals immediately jump to calculation methods without first considering available test data or the potential application of bridging principles.
Another common error is applying methods from the wrong level in the hierarchy. During a recent manufacturing audit, I reviewed a mixture SDS where the classifiers had applied bridging principles despite having complete test data for the specific mixture. This oversight led to incorrect hazard classifications that understated the mixture's corrosivity, creating potential safety risks for users.
Following the hierarchical approach is not merely about regulatory compliance—it's about ensuring the most accurate hazard classification based on the best available information. The sequence exists because test data for the complete mixture provides the most direct evidence of hazardous properties, while calculation methods involve more assumptions and potential uncertainties.
Stop Struggling with Complex Mixture Classifications
Don't wait for inspectors to find gaps in your documentation. SDS Copilot generates professional Safety Data Sheets in minutes with AI-powered mixture classification that automatically applies GHS bridging principles, cut-off values, and additivity calculations. Our system maintains a comprehensive audit trail of classification decisions and handles complex mixture formulations with ease.
Try SDS Copilot FreeBridging Principles: Classification Based on Similar Mixtures
When test data for the complete mixture is unavailable—which is often the case due to testing costs—bridging principles represent the next best approach. These scientific principles allow you to classify untested mixtures based on data from similar tested mixtures. However, these principles are frequently misunderstood and misapplied.
The Six GHS Bridging Principles
- Dilution: When an untested mixture is formed by diluting a tested mixture with a diluent that has an equivalent or lower hazard classification, the untested mixture can be classified in the same hazard category as the original tested mixture.
- Batching: Production batches of the same commercial product manufactured under controlled conditions can be assumed to have the same hazard classification.
- Concentration of highly hazardous mixtures: If a tested mixture is classified in the highest hazard category, then a more concentrated untested mixture should be classified in the same category.
- Interpolation within one toxicity category: For mixtures with identical ingredients but different concentrations, if Mixtures A and B are in the same hazard category, and Mixture C has concentrations of ingredients intermediate to Mixtures A and B, then Mixture C can be classified in the same category.
- Substantially similar mixtures: If Mixture A and Mixture B contain the same ingredients with only minor concentration differences, and Mixture A has been tested, Mixture B can be classified in the same hazard category.
- Aerosols: An aerosolized mixture can be classified in the same hazard category as the non-aerosolized mixture, provided the propellant doesn't affect the hazardous properties.
Common Bridging Principle Errors
In my consulting practice, I routinely encounter misconceptions about bridging principles. The most common errors include:
- Applying principles without sufficient reference data: You cannot apply bridging principles without comprehensive data on the reference mixture(s). Incomplete reference data invalidates the bridging approach.
- Ignoring principle-specific limitations: Not all bridging principles apply to all hazard classes. For example, interpolation applies specifically to acute toxicity but may not be appropriate for other hazard classes.
- Failing to document the rationale: When using bridging principles, you must document which principle was applied, the supporting evidence, and your justification for using that approach.
During a recent audit, I encountered a company that had applied the dilution principle for a corrosive cleaning product diluted with water. However, they failed to recognize that the dilution principle only applies when the diluent doesn't affect the hazardous properties of other ingredients. In this case, the water actually affected the pH of the mixture, invalidating the simple application of the dilution principle.
Ingredient-Based Classification: Cut-Off Values and Concentration Limits
When neither test data nor bridging principles are applicable, classification must rely on the known hazards of individual ingredients. This approach employs cut-off values and concentration limits—thresholds that determine when the presence of a hazardous ingredient triggers classification of the entire mixture.
Understanding Cut-Off Values
Cut-off values represent the minimum concentration at which a hazardous ingredient will trigger classification of the mixture for a specific hazard. These values vary by hazard class and category. For example:
- A mixture containing ≥1% of an ingredient classified as a skin corrosive (Category 1) will be classified as a skin irritant (Category 2)
- A mixture containing ≥5% of that same corrosive ingredient will be classified as a corrosive (Category 1)
- A mixture containing ≥0.1% of a respiratory sensitizer will be classified as a respiratory sensitizer
The application of cut-off values varies significantly across different hazard classes. Some hazard classes follow additivity principles (where the effects of multiple ingredients can be summed), while others follow non-additivity principles (where each ingredient is considered independently).
Additivity vs. Non-Additivity Approaches
One of the most critical decisions in mixture classification is determining whether to apply additivity or non-additivity approaches for each hazard class. Based on my experience:
Hazard classes that follow additivity principles include:
- Acute toxicity
- Skin corrosion/irritation
- Serious eye damage/eye irritation
- Specific target organ toxicity (single exposure) for respiratory tract irritation and narcotic effects
Hazard classes that follow non-additivity principles include:
- Skin sensitization
- Respiratory sensitization
- Germ cell mutagenicity
- Carcinogenicity
- Reproductive toxicity
- Specific target organ toxicity (repeated exposure)
During a recent formulation review, I identified a critical error where a manufacturer had applied additivity principles to carcinogenicity classification. They had several ingredients with carcinogenic properties below individual cut-off values and determined the mixture was not carcinogenic because the sum was still below the threshold. However, carcinogenicity follows non-additivity principles—each ingredient must be evaluated independently against the cut-off value.
Never Miss a Hazard Classification Again
Our AI-powered SDS Copilot automatically determines whether additivity or non-additivity approaches apply for each hazard class, ensuring accurate classification even for complex mixtures. Our system maintains comprehensive documentation of all classification decisions with full calculation transparency, providing defensible evidence of compliance during regulatory inspections.
Try SDS Copilot FreeAdditivity Formula Applications: Practical Examples
For hazard classes where additivity applies, GHS provides specific formulas that account for both the concentration and potency of hazardous ingredients. These calculations can be complex but are essential for accurate classification.
Skin and Eye Hazard Additivity
For skin corrosion/irritation and serious eye damage/eye irritation, the additivity formula takes the form:
∑ (ConcA / CLA) + (ConcB / CLB) + ... ≥ 1
Where:
- Conc is the concentration of a substance in the mixture
- CL is the concentration limit (generic or specific) for that substance
If the sum equals or exceeds 1, the mixture is classified for the corresponding hazard.
Example: Consider a mixture containing:
- 10% of Substance A (Skin Irritant Category 2, generic limit 10%)
- 2% of Substance B (Skin Irritant Category 2, generic limit 10%)
Applying the formula: (10%/10%) + (2%/10%) = 1 + 0.2 = 1.2 ≥ 1
Since the result exceeds 1, the mixture is classified as Skin Irritant Category 2.
Acute Toxicity Estimation (ATE) Calculations
Acute toxicity represents one of the most complex hazard classes for mixture classification. The approach uses Acute Toxicity Estimates (ATEs) rather than simple concentration percentages:
100/ATEmix = ∑ (Conci/ATEi)
Where:
- Conci is the concentration of ingredient i in the mixture
- ATEi is the acute toxicity estimate for that ingredient
Example: Consider a mixture containing:
- 1% of Substance X (oral LD50 = 225 mg/kg)
- 3% of Substance Y (oral LD50 = 100 mg/kg)
- 10% of Substance Z (classified in Category 3, ATE = 150 mg/kg)
Applying the formula:
100/ATEmix = (1%/225 mg/kg) + (3%/100 mg/kg) + (10%/150 mg/kg)
100/ATEmix = 0.0044 + 0.03 + 0.0667 = 0.1011
ATEmix = 100/0.1011 = 989 mg/kg
Based on this calculated ATE value (989 mg/kg), the mixture would be classified as Category 4 for acute oral toxicity (300 < ATE ≤ 2000 mg/kg).
In practical application, I've found that acute toxicity calculations are particularly prone to errors, especially when dealing with ingredients of unknown toxicity or when converting from LD50/LC50 values to ATE values. These calculations require careful attention to detail and thorough verification.
Handling Ingredients with Unknown Toxicity
A particularly challenging aspect of mixture classification is addressing situations where complete information on all ingredients is unavailable. This scenario is remarkably common, especially when dealing with complex formulations or ingredients sourced from suppliers who provide limited hazard information.
The 10% Rule for Unknown Acute Toxicity
For acute toxicity specifically, GHS provides guidance on handling ingredients with unknown toxicity. When the mixture contains ingredients of unknown acute toxicity:
- If the total concentration of ingredients with unknown acute toxicity is ≤10%, the standard ATE calculation can be used
- If the total concentration exceeds 10%, the calculation must be adjusted, or a statement about the percentage of the mixture consisting of ingredient(s) of unknown toxicity must be included on the label
During a recent consultation, I encountered a formulation where over 25% of the mixture consisted of ingredients with unknown acute toxicity. The manufacturer had simply ignored these components in their calculation, resulting in a significant underestimation of the mixture's hazards. The correct approach requires either a statement about the unknown percentage or the use of a modified calculation that applies a more conservative assessment.
Weight-of-Evidence Approach for Limited Data
When faced with incomplete data for other hazard classes, a weight-of-evidence approach becomes essential. This methodology involves evaluating all available information and making a reasoned judgment based on the totality of evidence.
Effective application of weight-of-evidence principles includes consideration of:
- Quality and reliability of available data
- Consistency of findings across different sources
- Relevance of data to the specific mixture
- Severity of potential hazards
- Conservative assumptions when uncertainty exists
When applying weight-of-evidence principles, thorough documentation is critical. Document not only your final classification decision but also the specific evidence considered, the weight assigned to each piece of evidence, and your reasoning process. This transparency is essential for defending your classifications during regulatory inspections.
Common Classification Errors and How to Avoid Them
Based on my experience auditing hundreds of SDSs, these are the most frequent mixture classification errors and their solutions:
1. Misapplication of Bridging Principles
Error: Applying bridging principles without sufficient data on reference mixtures or without meeting all conditions for their application.
Solution: Before applying any bridging principle, verify that:
- You have comprehensive data on the reference mixture(s)
- The specific conditions for the bridging principle are fully met
- The principle is appropriate for the hazard class being evaluated
- Your rationale is thoroughly documented
2. Incorrect Application of Additivity vs. Non-Additivity
Error: Applying additivity approaches to hazard classes that follow non-additivity principles (or vice versa).
Solution: Create a clear reference guide for your classification team indicating which hazard classes follow additivity principles and which follow non-additivity principles. Implement verification steps to ensure the appropriate approach is applied to each hazard class.
3. Calculation Errors in ATE Formulas
Error: Mathematical mistakes or incorrect input values when applying acute toxicity calculation formulas.
Solution: Implement double-check procedures for all calculations, preferably using automated tools or spreadsheets with built-in validation. Verify all input values against reliable source data before performing calculations.
4. Neglecting Specific Concentration Limits
Error: Using only generic concentration limits when specific limits have been established for particular substances.
Solution: Develop and maintain a database of ingredients with specific concentration limits. Ensure your classification process includes verification of whether specific limits exist for each ingredient.
5. Ignoring Ingredients of Unknown Toxicity
Error: Excluding ingredients with unknown hazard profiles from classification considerations rather than applying conservative approaches.
Solution: Implement clear protocols for handling ingredients with unknown hazards, including conservative assumptions when appropriate and clear documentation of the percentage of the mixture with unknown properties.
Documentation: The Foundation of Defensible Classifications
Thorough documentation of classification decisions is not merely a best practice—it's essential for regulatory compliance and defending your classifications during inspections. Based on my experience with regulatory audits, comprehensive documentation should include:
- Data sources: Identify all studies, databases, or supplier information relied upon
- Ingredient information: Record hazard classification, concentration, and any specific concentration limits for each ingredient
- Classification methodology: Document which approach was used (test data, bridging principles, or calculation methods)
- Calculations: Show all input values, formulas applied, and resulting outputs
- Assumptions: Clearly state any assumptions made, particularly regarding ingredients with limited data
- Weight-of-evidence decisions: Explain your reasoning when professional judgment was required
- Final classification determination: Summarize the resulting classification for each hazard class
I recommend establishing standardized templates for classification documentation that ensure all relevant information is captured systematically. These templates should become part of your standard operating procedures for SDS development and review.
Maintain this documentation throughout the product's lifecycle and update it whenever formulation changes occur or new hazard information becomes available. This ongoing maintenance ensures your SDS always reflects the most current understanding of your mixture's hazardous properties.
Conclusion: Beyond Compliance to Safety
Accurate mixture classification extends beyond regulatory compliance to the fundamental objective of protecting human health and the environment. By providing accurate hazard information through properly classified SDSs, you enable users to handle chemicals safely and implement appropriate protective measures.
The methodologies outlined in this guide provide a systematic framework for approaching the complex task of mixture classification. By following these approaches and implementing thorough verification and documentation processes, you can develop accurate, defensible classifications that support both regulatory compliance and the broader objective of chemical safety.
As global chemical regulations continue to evolve and harmonize, mastering these mixture classification methodologies becomes increasingly important. By investing in robust classification practices now, you position your organization for long-term compliance while fulfilling your ethical responsibility to communicate hazards accurately.
Remember that classification is not a one-time activity but an ongoing process that requires vigilance, expertise, and systematic procedures. As you refine your approach to mixture classification, you'll not only improve compliance but also contribute to a safer working environment for everyone in the chemical supply chain.